The Role of Gate Design in Improving Injection Mold Efficiency and Part Quality
5/14/20251 min read
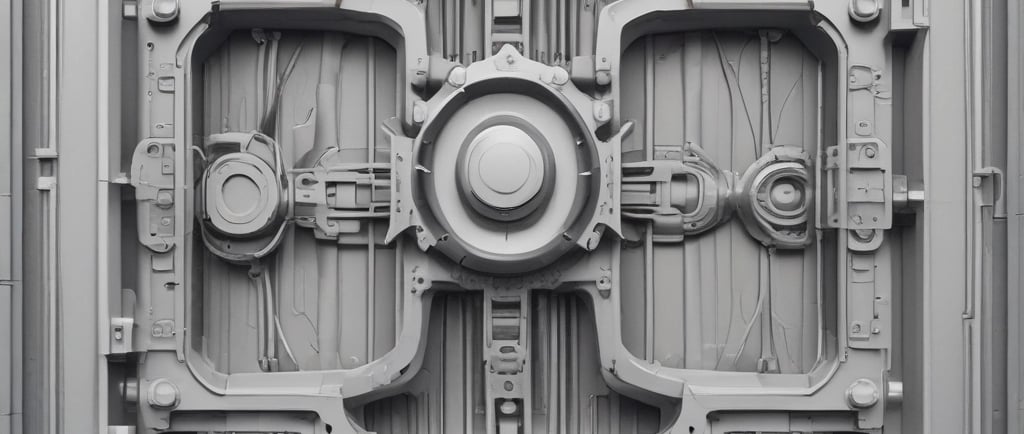
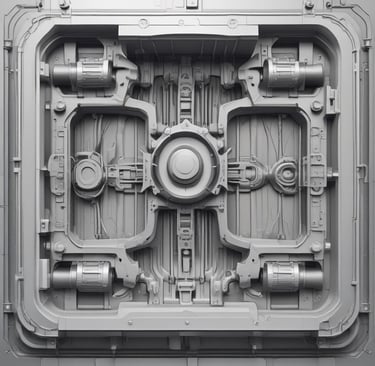
In injection molding, the smallest design features can have the greatest impact on product success. One of the most critical aspects is the gate design—the point where molten plastic enters the mold cavity. At Dongxinda Mould Technology Co., Ltd., we optimize every mold for performance, and that begins with gate engineering.
Why Gate Design Matters
Improper gate type or placement can lead to common defects like short shots, weld lines, warpage, and poor surface finish. That’s why our engineers perform full mold flow simulations to determine the best gate location and size, tailored to each part’s geometry, resin type, and production goal.
Types of Gates We Commonly Use:
Pin-point Gate: Ideal for multi-cavity molds, reduces visible marks.
Edge Gate: Excellent for flat parts and simple flow.
Submarine Gate: Allows automatic degating, suitable for high-speed cycles.
Hot Tip Gate: Used in hot runner molds for cosmetic surfaces.
Benefits of Optimized Gate Design:
Enhanced part strength and accuracy
Uniform material flow and shrinkage control
Shorter cycle times and less material waste
Better ejection and mold durability
Our team carefully balances the gate size with mold pressure and cooling channel layout to ensure perfect fill every time. Whether you’re manufacturing a small technical component or a high-volume consumer product, a smart gate design can transform your results.
FAQs:
Can you suggest a gate type based on my part model?
Yes, we provide free DFM feedback including gate recommendations.Do you offer hot runner system integration?
Absolutely, we design and build both cold and hot runner molds.What if I already have a gate issue?
We can evaluate and modify existing molds to improve flow and reduce defects.
One-stop service for all your molding needs.
contact information
+65 80391511
+86 13860465777
© 2024. All rights reserved.